Inside the military, everyone is expected to be tough. The gadgets and computers utilized in this field are also a factor, in addition to the hardworking workers. Naturally, this calls for circuit boards utilized in the defense industry to be rock-solid.
What Does Mil Spec Mean?
Some persons may employ the phrase “Military Spec” carelessly in order to suggest that their tool or product is more durable than the competition’s. What we mean is that, In other words, the term now refers to any product that goes above and beyond what the average buyer would expect.
Firstly, what exactly is mil-spec? The military is related to mil-spec. It serves as the standard for the military.
Every aspect of the military is standardized so as to promote dependability, interoperability, as well as system commonality. This enables the military to replace parts in perhaps the most inconvenient locations at the drop of a hat. The specifications which the military had established for that specific component are known as mil-spec. The government often owns the design rights to the component.
The term “military specification” is well-defined in its meaning. It is only applicable to goods created in accordance with guidelines established by military associations and committees and managed by them to assure compliance.
Also, other industries that require equipment to function flawlessly in challenging circumstances also have highly strict manufacturing requirements. So, among other things, we find requirements for the aerospace and medical industries.
Basic Design Features for Mil Spec PCBs
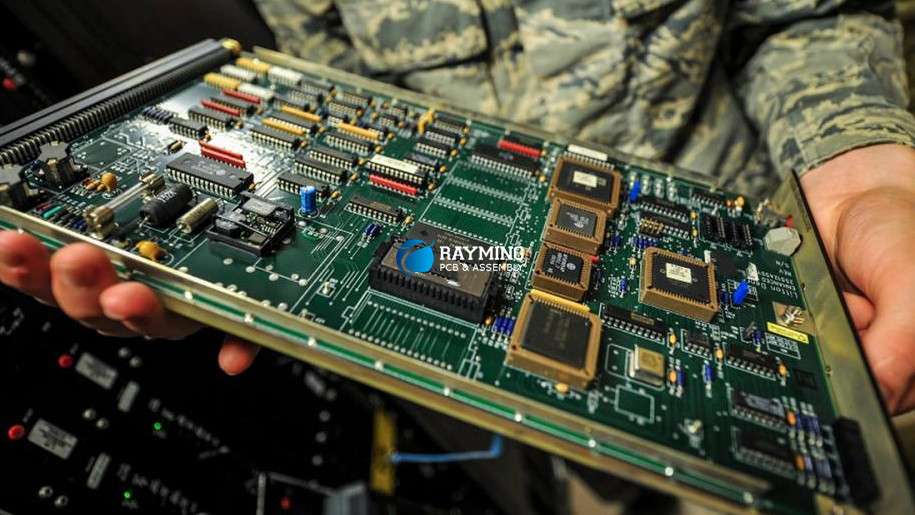
All PCBs belonging into this category must meet MIL spec PCB requirements and successfully complete the most stringent functionality and performance testing. Considerations for the mil spec PCBs in general include:
They should be able to handle the highest current load. High-frequency and low-frequency components should be distinguished clearly. A few high-frequency components, for instance, might generate waveforms which might influence those low-frequency components. The waveforms could increase noise and degrade the signal’s quality. This is intolerable to the military.
- All the clock signals must to be pristine and protected.
- All PCB routings must be kept at an angle of 45° or less for seamless current transmissions.
- Finally, MIL-PRF-50884, MIL-PRF-31032, and MIL-PRF-55110 standards should be strictly followed when manufacturing any PCBs for use in military applications.
Considerations for Mil Spec PCB Design
Materials
When developing and producing mil spec PCB, you should take into account the best types of PCB substrate after becoming familiar with the design specifications.
The table should only be made of the highest quality, heat-resistant materials. Electronics built for the military are frequently used in harsh environments, including hot temperatures. Even under these circumstances, the PCBs ought to be resilient and capable of good performance.
Thermal compounds must be utilized whenever heat dissipation would be required. Consideration should be given to the materials and finishes. They ought to help the PCB function effectively in challenging environmental circumstances.
Extremely durable materials which can survive harsh conditions and temperatures seem to be essential. At this point, having a solid understanding of various composites, substrates, as well as components to employ in PCBs is crucial.
To qualify as military-grade, they must adhere to strict stiffness, flexibility, electrical, as well as thermal specifications. The following are some ideal materials for usage in mil spec PCBs:
- Aluminum
- High-temperature laminates
- Copper
Anodized aluminum can also be employed occasionally to reduce the consequences of the heat-induced oxidation.
Treatment of the Surface and Coating

For surface treatment that can shield the PCBs from harmful external factors including dust, vibration, water, and severe temperatures, the military does have certain specifications. As a result, surface treatments and coatings are crucial components of military-grade electronics. PCBs are shielded from rust by copper coatings.
There are many materials for surface treatment available based on the function of the Circuit board. These include lead-free HASL, immersion silver, and more. The PCB may also be conformally coated with sprays with an acid- or acrylic-based base to further protect them from the elements.
Durability
The military’s top priorities are dependability and durability. More so since the parts are utilized in less-than-ideal circumstances and are vulnerable to deterioration, including solder cracking.
Military electronics typically last 5 to 15 years, therefore ensuring their endurance, dependability, and longevity necessitates reducing the mounted component’s vibration.
Through-hole mounting seems to be the suggested technique of installation during circuit board assembly for various military grade PCB. The boards produced with this method are quite robust. Additionally, the technique uses soldering out from bottom and top of the circuit board to fortify the physical connections between the parts as well as the board.
What Characterizes the Mil Spec PCB?
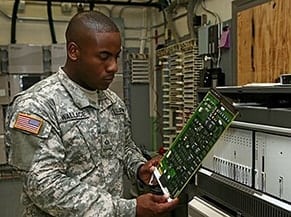
A skilled eye can easily distinguish between IPC Class 3 or mil spec PCBs and industrial or commercial IPC Class 2 or 1 PCBs. Let’s look more closely.
Planning a test
The IPC Class 3 Circuit boards are “Integrated for Test,” which is an official designation that denotes a focus on making components accessible so they may be tested separately from the other equipment they interact with. Where possible, components are placed for simple replacement and removal and test points were moved to the PCBs’ outer edges.
Superior Components
All IC Class 3 projects must include the best possible components, which must be specified. All of the parts must function with incredibly tight tolerances and be completely reliable. It is best practice to be quite particular about these components that will be installed on the circuit board since there’s no tolerance for average and approximate performance. Instead of using a general description, provide the manufacturer as well as part numbers. Very Rugged
Mil Spec PCBs are made to withstand harsh conditions. They must be constructed with robustness and dependability as their top priorities in order to accomplish this.
It is desirable to have thicker cores as well as broader layer spacings. Problems involving component isolation, heat dispersion, PCB thermal expansion, and fundamental physical strength are brought on by thin cores.
Conclusion
It’s really no secret that PCB design concerns for military-grade electronics are complicated. Make sure that the ECM you work with is both fully accredited and certified and also has the necessary experience.
Related posts:
- Design Considerations and Material Selection for High Voltage PCB Design
- What are the Applications and Design Considerations of the Robot PCB?
- What are the Benefits and Design Considerations of the HDI Multilayer PCB?
- Three Features of the Cadence PCB Designer Standard that Supports Customized Engineering Design and Prototyping