Printed circuit boards are core components of all electronic devices. They serve an important role in revealing the functioning and performance of an electronic device. On these boards are electronic components mounted on. These boards create electrical connections between components and offer mechanical support. PCBs are usually fabricated to meet the requirements of the applications for which they would be used.
Some particular kinds of printed circuit boards can be more complex and challenging to fabricate compared to others. These kinds of PCBs would need more steps in their manufacturing process. A good example of such boards is high tech PCB. High technology PCBs are more complex to fabricate. This is because these boards can feature high layer counts, can be made out of exotic materials, and may need additional fabrication and design processes with tighter tolerances.
What is a High Tech PCB?
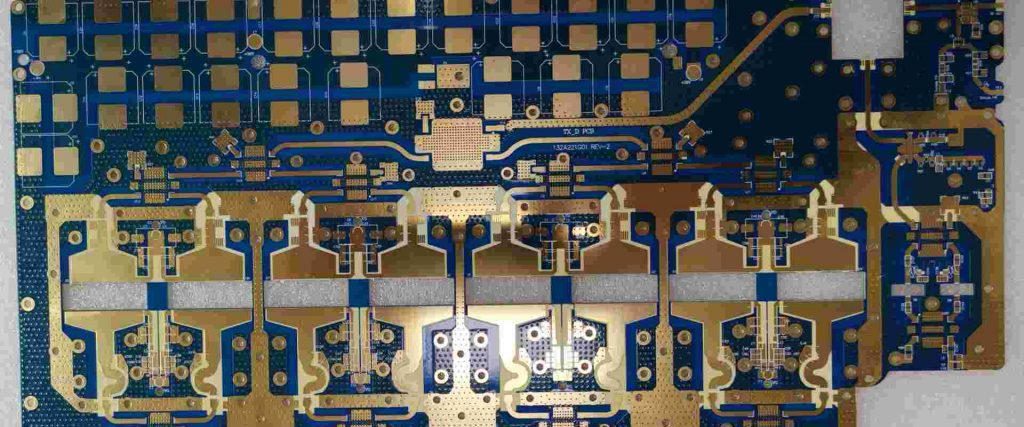
A high tech PCB is a type of circuit board that requires complex fabrication process. A circuit board is classified as a high tech PCB based on some factors. These could be the number of layers, the material used in fabricating them, the feature they offer, the technology used in fabricating these boards, and more.
There are good examples of a high tech PCB. Examples include ceramic PCB, multilayer PCB, High density interconnect PCB, flexible PCB, and rigid-flex PCB. A high tech PCB requires technical experts to manufacture since there are fabrication processes require strict attention. Also, it is important to note that this kind of PCB is usually fabricated with high demands.
It is only possible to fabricate a high technology printed circuit board if it is made of industry standard materials. Furthermore, the design and fabrication processes are usually well-defined. It is important to check every process is for the expiry of the treatment period.
It is ideal to check the quality of the material, mechanical features, and the shape of the holes of a high tech PCB. The design and manufacturing process of a high tech PCB is very complex and as such PCB manufacturers need to pay attention to these boards.
Characteristics of High Tech PCB
A high tech PCB has some characteristics which differentiate them from a regular circuit board. Some of their characteristics are explained below
High quality base material
The capacity of a high tech circuit board to conduct electrons is one of the characteristics of a high-tech PCB. The base material of this circuit board must be made of advanced quality. This is because high tech PCBs are often used in applications that are quite demanding. Therefore, this board must be able to withstand whatever it will go through in it’s operational environment.
Also, a high tech board with good quality PCB base material prevents problems such as delamination, open circuit, and more. Therefore, the base material must undergo appropriate testing before it is being used.
Impeccably clean PCB
High tech printed circuit boards should never have a speck of dust or any dirt on their surface. This PCB should be absolutely free of dust and any solder resistant material. Poor connection or bad solder joints may occur If the material is not properly clean and free of dirt.
Positional Tolerance on PCB
A high tech printed PCB should have well-defined vias, tolerance of drill holes, tracks, and other physical and mechanical features. This makes this board distinct and scores high in terms of performance and appearance. The hole size and some other features are very crucial and it is important to define their tolerances. As regards this, the purpose is not to subject the printed circuit boards to stress test. However, the purpose is to be sure these specifications are well integrated exactly as per the limitations defined.
Tolerant copper clad made based on international Standards
A high tech PCB should feature a copper cladding that meets the tolerance standards established under quality criteria. This is very crucial in this circuit board as ensures more control on the dielectric layer thickness.
A thick dielectric layer minimizes the deviation in expected value of performance. Furthermore, it is important to pay attention to quality of components since the copper cladding alone can’t perform as expected.
High-quality PCB Treatment
The treatments performed on circuit boards during fabrication don’t last forever. Therefore, it is very crucial to be sure there is no change in the surface treatment at the time of employing the high tech printed circuit board.
It is crucial for high tech printed circuit boards to undergo a series of quality tests before they are being integrated. Furthermore, when a PCB surface treatment goes beyond its shelf life, there is a tendency for the circuit board to suck moisture and as such makes soldering a much more difficult process. Furthermore, this will increase the risk of circuit break and de-lamination.
Thick solder resist layer
While there are no exact provisions for the thickness of solder resistance defined in IPC, the solder resist layer need to have a good level of tolerance needed to support electrical insulation. A tolerant thick solder resist layer helps to minimize the chances of peeling and as such makes the high tech PCB develop more tolerance towards any mechanical impact.
The solder resist layer may peel off of it is not thick enough and this may expose the copper in the high tech PCB to corrosive agents around. In the long run, this results in poor insulation. Therefore, a high technology PCB must have a thick solder resist layer.
Types of High Tech PCBs

There are various types of high tech PCBs. As it was earlier explained, these circuit boards have unique characteristics.
High density interconnect (HDI) PCBs
HDI circuit board features greater circuitry density for each unit. The circuitry density for this board is higher than that of conventional boards. Also, HDI PCB integrates both blind and buried vias. This board also integrates microvias which are 0.006″ or less in diameter.
High-density circuit board is classified as a high tech PCB. This board has buried and through vias. Also, HDI board features substrate constructions without electrical connection.
HDI printed circuit boards played a crucial role in the manufacturing of many of today’s electronic devices, particularly those that have smaller size and less weight. This board is responsible for the decrease in the size and weight of some devices. A smaller device is more likely to integrate a HDI PCB.
HDI boards have tight tolerances and as such the fabrication process of these boards must be handled by an experienced manufacturer. The slightest defect or layout errors can result in significant problems.
RF/Microwave PCB
RF/microwave PCB is a tech PCB. This board comprises components that transmit RF or microwave signals. The signals transmitted by this PCB signals vary in terms of frequency. Their frequency ranges from 50MHz to more than 2 GHz.
The frequency at which RF or Microwave PCB operates differentiates them. While a microwave PCB operates in a frequency more than 2Ghz, a radio frequency RF PCB operates in a frequency above 100MHz.
RF/Microwave PCBs are more complex to design compared to conventional PCB layouts. This is because of the challenges being faced with when receiving or transferring radio signals. Tighter impedance tolerances and noise sensitivity are some of the main problems with this board.
RF/microwave PCBs are more sensitive to noise and as such require tighter impedance tolerances. When designing a RF/microwave PCB, the best solution is to integrate ground planes. Also, you can make use of a bend radius on traces that have impedance control. With this, the RF/microwave board can perform better.
The material selection of RF/microwave boards is crucial in determining their performance. This is because these boards are specially designed to function at certain frequencies. Advanced composites are used in building RF/microwave PCBs. These composites feature particular properties for coefficient of thermal expansion, dielectric constant and loss tangent.
Rigid PCBs
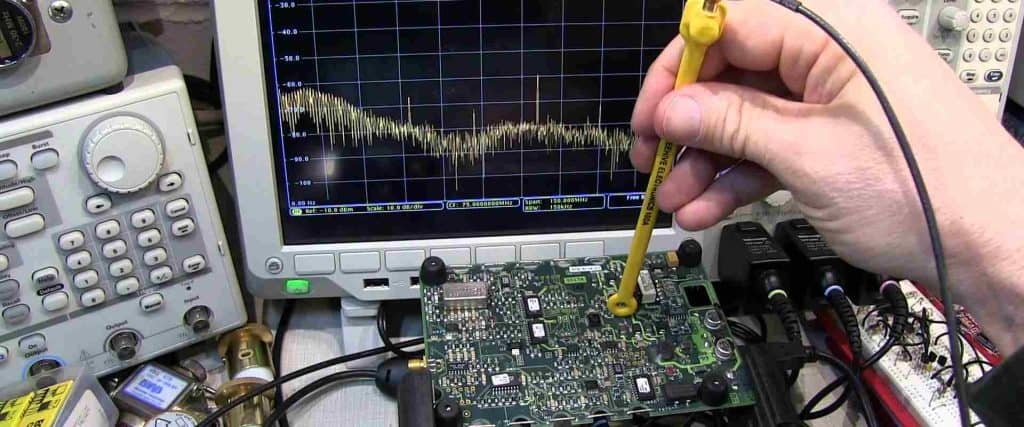
A rigid board is a type of printed circuit board which has a solid substrate for its base material. This board is a good example of high tech PCB. The solid substrate material prevents the distortion of the PCB. A rigid circuit contains several layers combined with the used of heat and adhesive. The substrate layer of this board is usually made of fiberglass.
FR4 is the most common material used as the substrate of this board. This is because of the sturdiness and rigidity of these materials. In some cases, epoxies and phenolics are used as the base materials. These materials aren’t as efficient as FR4, but, they are less costly.
A rigid PCB can’t be folded or twisted to form any shape due to the FR4 reinforcement in this circuit board. A good example of rigid circuit board is the computer motherboard. Rigid circuit boards are resistance to aggressive oils, chemicals, and even radiation. Therefore, these boards are ideal for use in hostile environments.
The properties of these boards can be enhanced to resist shocks, stresses, and vibrations. Rigid boards are widely integrated in applications that require high performance. For instance, they are ideal for use in industrial applications. However, the manufacturing process of these boards is very complex.
High speed PCB digital
High speed circuit boards comprise microprocessors and other components that manage billions of operations every second. These boards need to be properly designed and manufactured to minimize errors. The integrity of signals can affect the physical characteristics of high speed PCB. Designing a high speed PCB is complex due to some issues that arise. In a simple circuit design, manufacturers might pay attentions to simple issues like routing and component placement.
The design process of a high speed board requires considering some factors like the width of the PCB, placement of traces, how close it is to signals, and what type of components they are connected to. a high speed circuit board is commonly used in applications like network communications, medical equipment, consumer-facing installed electronics.
High speed PCBs require high speed routing. Routing traces with impedance control is crucial in high speed designs. Antennae and differential pairs are impedance characteristics for high speed PCBs. PCB designers need to understand how layer stack and trace width are calculated for impedance values. There may a negative impact on the signal of high speed PCB, if the impedance values are incorrect.
Applications of High Tech PCBs
High tech PCBs are used in high frequency and high performance applications. These boards find their use in devices that are usually subjected to shock, vibration, and high temperature.
Safety and security equipment
There are several aspects of security systems that depend on a high tech PCB. These systems are crucial for the safety and security of human lives and properties. Some safety and security device such as electronic door locks, security cameras, and smoke detectors integrate high technology boards. Modern safety equipment make use of high technology boards.
Military and defense applications
Printed circuit boards used in military devices are usually subjected to a high level of shock, vibration, and extreme temperature. Therefore, the circuit boards integrated in this application need to be extremely durable and reliable. The military make use of high tech PCBs since these boards comprise high-temperature laminates, copper, and other materials. Control systems and communication equipment used in the military comprise high tech PCBs.
Aerospace components
Aerospace devices need high tech PCBs. They need PCBs that comprise materials that can tolerate vibration and other harsh conditions. Also, some aerospace device function in the outer space and as such, they must be very durable.
Industrial equipment
Another use case of high tech PCB is in the industrial equipment. The circuit boards integrated in industrial machines and devices need to high-powered. Also, they must have the ability to withstand some harsh conditions. These boards must have resistance to extreme temperatures, harsh chemicals, and rough handling. To meet these needs, the industrial sector needs to make use of high tech printed circuit boards.
Conclusion
High technology PCBs are more complex to fabricate. This is because these boards can feature high layer counts, can be made out of exotic materials, and may need additional fabrication and design processes with tighter tolerances.