A Big Switch PCB (Printed Circuit Board) is a type of circuit board designed for handling high power applications. As the name suggests, a Big Switch PCB is used to control and regulate the power flow in equipment that needs to operate at high voltages or currents.
Some typical applications where Big Switch PCBs are used include:
- Motor drives
- Inverters
- Power supplies
- UPS systems
- Solar and wind power systems
- Battery chargers
- Industrial automation and control systems
Compared to a standard PCB, a Big Switch PCB is engineered to handle much higher power levels safely and reliably. They allow equipment manufacturers to control and convert high voltages/currents efficiently through carefully designed high power components, traces, and layout techniques.
Key Characteristics of a Big Switch PCB
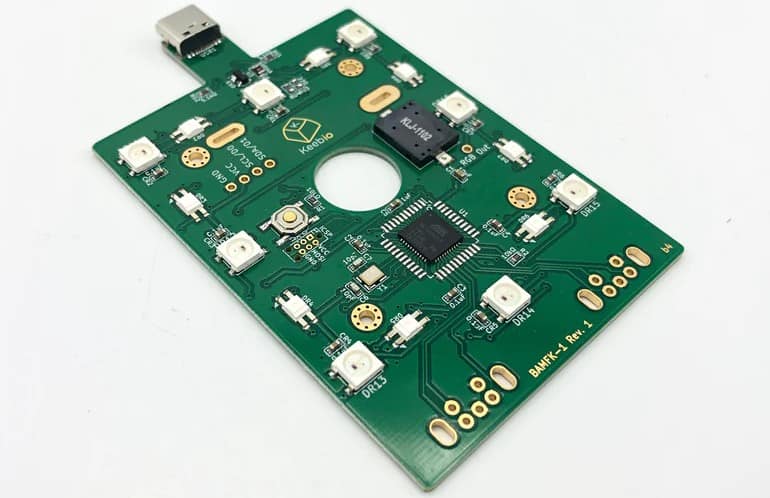
Some of the key characteristics and design considerations for Big Switch PCBs include:
1. Voltage and Current Handling Capability
Parameter | Typical Value |
---|---|
Voltage | 300V to 1500V |
Current | 10A to 800A |
They are designed to handle voltages ranging from a few hundred volts to over a thousand volts. Similarly, these boards can carry high DC or AC currents from 10A to 800A comfortably.
2. Layout Design
The PCB layout for a Big Switch board needs to ensure adequate isolation, spacing, and heat dissipation for the high power components. Key factors include:
- Generous spacing between high voltage traces/components
- Solid power planes for heat spreading
- Adequate isolation for voltage domains
- Thermal vias and pads for heat dissipation
- Reinforced solder joints
3. Components Used
Components designed specifically to handle high voltage/current are used, including:
- IGBTs – Insulated Gate Bipolar Transistors
- MOSFETs – Power MOSFETs
- High power transformers/chokes
- High voltage capacitors
- Overvoltage protection devices
- High power connectors
- Current sensors
4. Safety and Protection Circuits
Multiple safety mechanisms are incorporated into Big Switch PCB designs:
- Fuses
- Suppressors to limit voltage spikes
- Snubber circuits to reduce switching losses
- Thermal shutdown to prevent overheating
- Independent voltage/current monitoring
5. Form Factor and Layer Count
These boards tend to be larger in size and have higher layer counts for better heat dissipation and routing capability. Common specs are:
- 6 to 12 copper layers
- Board sizes up to 600mm x 600mm
- 2 oz copper thickness or above
Manufacturing Big Switch PCBs
Manufacturing quality Big Switch PCBs require stringent process controls and testing methods to ensure reliable performance in the field.
1. Base Materials
Highly thermally conductive dielectric materials like IMS or ceramic substrates are used which can withstand high temperatures.
2. Copper & Plating
To handle high currents, thick copper of 2oz/ft2 or above is preferred. Plated edge connectors provide durable high current terminals.
3. Test & inspection
100% automated optical inspection (AOI) and bare board testing is done. Steps include:
- Net connectivity testing
- High voltage testing
- Clamping force measurement
- Thermal stress testing
- Visual inspection at multiple stages
4. Qualifications
Big Switch PCB suppliers must have suitable qualifications for manufacturing high reliability boards. Typical credentials include:
- IATF 16949 certified
- AS9100 certified
- IPC 6012 Class 3 qualification
5. Supply chain control
Stringent supply chain norms ensure traceability and integrity of materials used. Procedures like counterfeit component avoidance are followed.
Applications of Big Switch PCBs

Some of the major applications where these high power PCB are commonly used include:
1. Motor Drives
Variable frequency motor drives use Big Switch PCBs to control AC motors through IGBTs and rectifiers. They allow smooth and efficient variable speed operation.
2. Switch Mode Power Supplies
High efficiency switch mode power supplies use these boards for creating tightly controlled and regulated DC outputs from an AC source.
3. Inverters
Solar, wind and battery inverters use Big Switch PCBs with high power IGBTs to produce grid-quality AC power from a DC source.
4. Battery Chargers
High capacity rapid electric vehicle chargers and battery charging systems rely on these boards to quickly and safely charge the batteries.
5. Lamp Ballasts
Fluorescent and HID lamp ballasts use Big Switch PCBs to provide controlled high voltages to light the lamps.
Some other applications include UPS systems, plasma cutting equipment, welders, etc. In essence, any power electronic systems dealing with high voltages or currents requires Big Switch boards.
Benefits of Using Big Switch PCBs
Some of the major benefits obtained by using custom engineered Big Switch PCBs are:
1. Increased Safety: Careful layout, protection circuits and testing ensures safer high power operation.
2. Higher Reliability: Robust components, thermal management and process controls helps achieve field failure rates < 1 per million hours.
3. Smaller Size: Greater power densities minimizes footprint and weight.
4. Better Efficiency: Optimized and low-impedance layouts improve efficiency by 3-5%.
5. Cost Savings: Higher reliability, better manufacturability and shorter development time provides overall cost benefit.
Selection Criteria for a Big Switch PCB Manufacturer
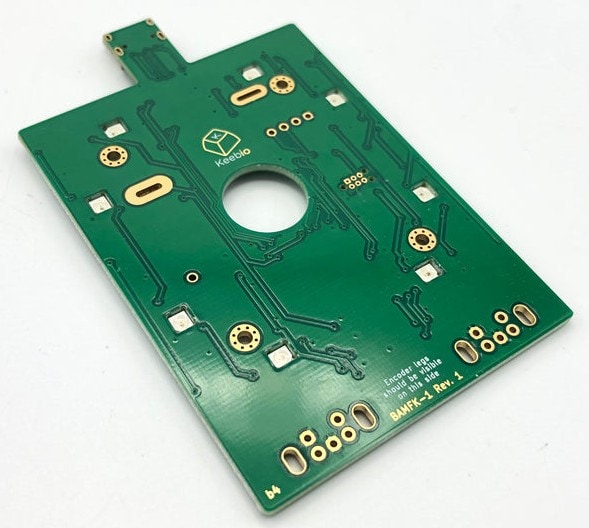
When outsourcing Big Switch PCBs, partnering with the right manufacturer is key for ensuring optimal quality, performance and reliability. Some of the top criteria in selecting a supplier include:
1. Technical Capability: Possession of latest PCB technologies and high layer count capability with suitable testing.
2. Quality Systems: Certified management systems like ISO9001/IPC that ensure consistency.
3. Qualifications: Relevant qualifications such as IPC 6012 Class 3 and AS9100 prove technological competence.
4. Field Failure Rate: Look for proven track record with field failure rates < 20 PPM.
5. Responsiveness: Quick turnaround on prototype builds with excellent engineering support speeds up projects.
6. Cost Effectiveness: The right blend of quality, reliability and affordability ensures a prudent choice.
Frequently Asked Questions
Q1. At what voltages should you consider using a Big Switch PCB?
Generally once the voltages exceed 200V it is recommended to use a custom Big Switch PCB over a standard PCB for better safety and reliability. The exact threshold depends on current levels too – for example, 100V could still require a Big Switch design if current load is >100A.
Q2. Does the size of a Big Switch PCB impact its performance?
Yes, generally larger sized Big Switch boards with adequate spacing between components perform better. A larger surface area allows for better thermal dissipation. However, size constraints are common in product design. In such cases, designers employ other techniques like thermal vias, special substrates etc. to maximize power density.
Q3. Can you use a Big Switch PCB at higher than rated voltages temporarily?
It is normally not advisable, as running the board above its rated voltages risks immediate or latent damage to components. Designers keep safety margins of 20%+ beyond rated voltages. Repeated over-voltage exposures should be avoided even if board seems to operate normally after temporary spikes.
Q4. What are common design mistakes to avoid in Big Switch PCBs?
Some common pitfalls include underestimating power losses, insufficient isolation between high-voltage domains, ignoring thermal design, resonant tank issues, ignoring inrush current effects, under-rating of components, and lack of protection for transients. Cross-checking the design before layout by an expert PCB designer minimizes such issues.
Q5. Does environmental testing like shock/vibration apply to Big Switch PCBs?
Yes, certain big switch boards used in high reliability or defense applications require additional environmental testing as per standards like MIL-STD-810. This ensures the PCB assembly can survive shock, vibration, thermal shock, salt fog and other harsh conditions experienced over product’s service life without field failures.