Printed circuit boards (PCBs) are delicate and sensitive electronic components that require proper handling and storage. PCB racks, holders and trays are specifically designed to organize, protect and secure PCBs during manufacturing, assembly, testing, storage and transport. Selecting the right racking and storage solutions can safeguard PCBs against physical damage as well as electrostatic discharge. This guide provides a comprehensive overview of the different types of racks, holders and trays available for PCB applications.
PCB Racks
PCB racks provide slots or open spaces to hold multiple PCBs vertically in an organized manner. They allow easy insertion and removal of boards for access.
Rack Construction
- Made of plastic or metal
- Provide mounting holes to attach to worktable or enclosure
- Some models have anti-static coating or dissipative plastics
Rack Types
- Open frame racks – basic racks with open slots to insert PCBs
- Enclosed racks – completely enclosed with transparent door to protect boards
- Card cage racks – for vertically mounting PCBA cards
- Magazine racks – allow stacking of PCBs like a magazine
- Slotted rails – rail-based structure with slots to hold PCBs
Key Benefits
- Organized vertical storage to systematically access each board
- Saves benchtop space compared to laying PCBs flat
- Allows mounting multiple PCBs of same type for production
- Protects boards from physical damage
- Some racks provide electrostatic discharge (ESD) protection
Applications
- PCB storage and transport
- Programming and testing
- PCB assembly line workflow
- Board burn-in testing
- Field servicing of equipment
PCB Holders
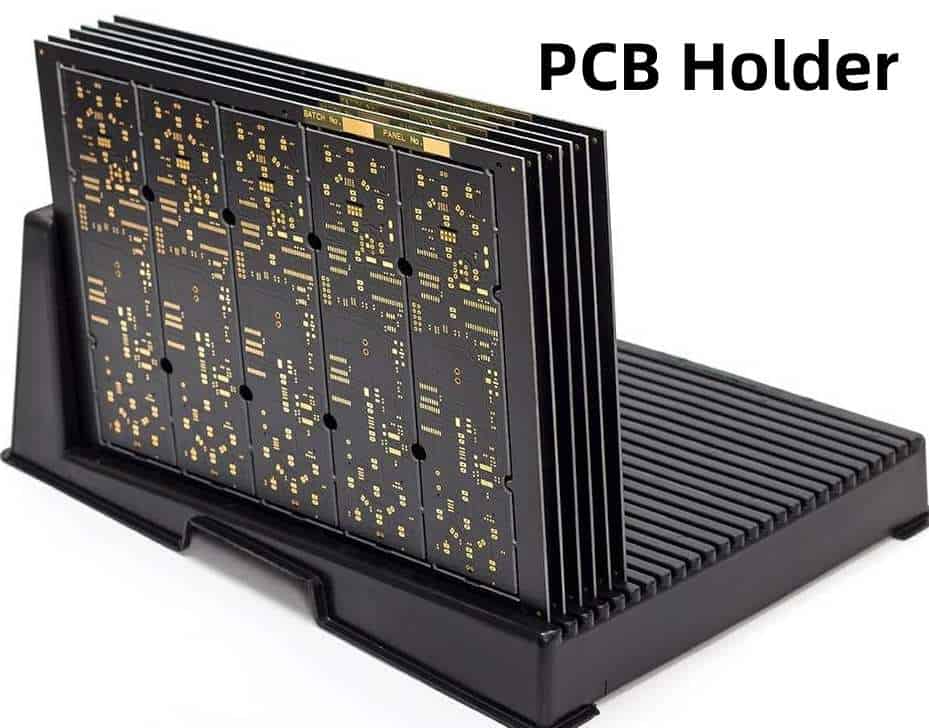
PCB holders securely retain a single PCB to protect it during handling, testing and processing. They prevent physical stress and abrasion damage.
Holder Construction
- Made of plastic or metal
- Have retaining clips, screws or friction rails to lock the PCB
- Standoffs separate PCB from base
Holder Types
- Clip-on holders – plastic holders with clip on top to retain PCB
- Screw-down holders – metal plates compress PCB between screws
- Sliding holders – plastic holder with sliding rails to lock PCB
- Pogo pin holders – provides electrical test contact with pogo pins
Key Benefits
- Protects PCB from bending and flexing stress
- Provides secure mounting for handling and processing
- Compatible with soldering, cleaning and testing processes
- Allows electrical edge connector access to PCB
- Some holders made of anti-static materials
Applications
- PCB hand assembly
- Soldering and de-soldering
- Cleaning and coating
- In-circuit testing
- Burn-in testing
- Programming finished boards
PCB Trays
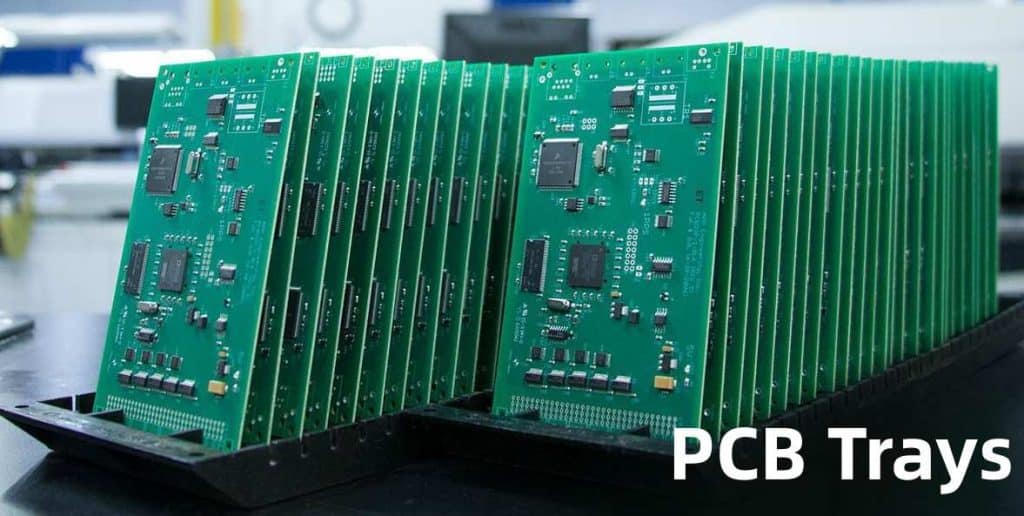
PCB trays provide flat protective carriers to hold PCBs horizontally without bending or warping the boards. They are used for storage, transport and PCB processing.
Tray Construction
- Made of plastic or other polymers
- Have divider ribs to separate each PCB
- Anti-static conductive or dissipative polymers used
Tray Types
- Universal trays – grid of adjustable dividers to fit various PCB sizes
- Custom trays – molded trays fitted for specific PCB outline
- Jedec trays – standard trays for handling ICs and chips
- Magazine trays – stackable trays like a magazine
Key Benefits
- Protects PCB surface from scratches
- Prevents board warpage over time
- Organized compartmental storage
- Trays stackable for space efficiency
- Anti-static material prevents ESD damage
Applications
- PCB storage in warehouses
- Transporting PCBs between facilities
- Buffer storage on PCB assembly lines
- Work-in-progress storage during manufacturing
- Protecting finished PCB assemblies
Specifications
Key specifications to consider when selecting PCB racks, holders and trays:
Material
- Plastic – polycarbonate, acetal resin, PTFE
- Metal – aluminum, steel, stainless steel
- Anti-static – dissipative or conductive polymers
PCB Capacity
- Rack slots or holder openings for different PCB sizes
- Trays have adjustable divider configurations
ESD Protection
- Anti-static coatings and polymers
- Grounding features and wrist straps
Temperature Rating
- Withstand soldering heat up to 350°C
- Meet PCB cleaning and processing temperatures
Physical Dimensions
- Overall outer dimensions
- Rack slot pitch and spacing
- Holder opening dimensions
- Tray compartments size
Selection Criteria
Consider the following factors when selecting the optimal PCB racks, holders and trays:
PCB Size and Quantity
- Racks and trays should fit PCB footprint
- Determine number of PCBs to be stored
Required Protection Level
- Open racks vs. enclosed racks vs. protective trays
- Needed during transport, storage, or processing?
Physical Conditions
- Environmental temperature and humidity
- Will racks/trays encounter vibration or shock?
ESD Safeguarding
- For handling static-sensitive boards
- Level of ESD control needed
Mounting and Access
- How will racks be mounted? On benchtop or enclosure?
- Easy PCB insertion/removal required?
Budget
- Open frame racks more economical
- Enclosed racks and custom trays cost more
Advancements in PCB Racks and Storage

Recent improvements in PCB racking, holders and trays include:
- Ergonomic designs: Easier handling and access to boards with slide out trays, rotating racks and adjustable working heights.
- ESD protection: Conductive polymers, dissipative coatings and grounding features built-in.
- Modular racks: Separate vertical slotted panels can be joined to hold different PCB sizes.
- Smart rack monitoring: RFID tags monitor PCB locations. Sensors track environmental conditions.
- Quick-change tooling: Faster and simpler changeover when switching PCB designs.
- Automated racking: Robotic pick-and-place systems to insert and remove PCBs from racks and trays.
Key Benefits of Using Proper Racks and Trays
Utilizing purpose-built PCB racks, holders and trays offers important benefits:
- Protects boards from physical damage like bending, vibration, abrasion.
- Safeguards PCBs from ESD damage during handling and storage.
- Eliminates tangled cables and wires hanging off loose boards.
- More organized inventory and smoother workflow.
- Increased PCB quality with lower defect rates.
- Saves production time compared to improvised storage methods.
- Safer transport between production stages without board damage.
- Ergonomic racks reduce worker fatigue and injuries.
Storing Sensitive PCB Assemblies
PCBs with sensitive components require specialized storage:
- Moisture-sensitive boards – Use dry storage cabinets or bags with desiccant to avoid moisture absorption.
- Photonics PCBs – Protect photonic components from light exposure with opaque antistatic foam or dark trays.
- High voltage boards – Prevent arcing with non-conductive trays rated for required voltage separation.
- High frequency boards – Shielding may be needed to block external RF interference.
- High temperature boards – Use high temperature polymers or ceramics resistant to soldering heat.
Example PCB Racking Systems
Here are some examples of complete racking systems to handle PCBs through the manufacturing process:
Storage and Transport Racking
- Trays to store populated or bare PCBs.
- Slotted rail racks to hold boards vertically for staging.
- Move PCBs on carts between production areas.
- Anti-static plastic construction.
Soldering and Washing Racks
- Frame holder secures PCB for hand soldering.
- Transfer boards to wash racks for cleaning process.
- Compartment trays separate different wash batches.
Testing and Programming Racks
- Clamshell ESD-safe holder for in-circuit testing station.
- Indexing rack inserts boards into programming fixture.
- Rack feeds tested boards to final packout.
Frequently Asked Questions
What are some tips for using PCB racks and trays?
- Label rack slots and trays clearly for easy identification.
- Use marker strips to indicate empty slots needing replenishment.
- Insert boards gently without bending or forcing.
- Cover unused rack openings to keep out debris and dust.
- Lock rack casters when stationary to prevent rolling.
How can I estimate the size of rack needed?
Determine number of boards and production rate. Allow space for future requirements. A 12 or 24 slot rack is typical for small volumes. Multiples of 24 slot racks are common in production.
What design files do vendors need to create custom racks?
Supply the PCB outline drawing, preferably in dxf format. Indicate required slot pitch and quantity. List special needs like ESD protection. State expected lifetime usage.
Should racks used in wave soldering have special coatings?
Yes, racks and trays in soldering processes require high temperature coatings that withstand soldering without degrading. Fluoropolymer impregnated anodized aluminum is a common choice.
How often should I audit our PCB racks and storage?
Perform regular checks of racks and trays to ensure they remain undamaged and contaminant free. This prevents them from causing defects. Replace racks showing signs of wear. Review ESD protection and grounding.
Conclusion
PCB racks, holders and trays are critical investments to protect delicate electronics boards throughout manufacturing stages. This guide reviewed key types, specs and selection criteria to choose optimal solutions that organize and safeguard PCBs during production, storage, assembly and testing. Leveraging purpose-built racks, holders and trays improves workflow, productivity and first pass yields when dealing with large volumes of PCBs. They reduce costly board damage and ESD events. With careful selection using the principles outlined here, you can implement racks and storage that increase throughput, lower costs and deliver higher quality boards.