Introduction
Microwave printed circuit boards (PCBs) operate at microwave frequencies from 300 MHz to 300 GHz to enable radar, telecommunication, navigation, medical and other RF systems. Fabricating PCBs for these extreme high frequencies requires specialized materials, processes and testing capabilities. This article explores the top 10 global manufacturers of microwave PCBs based on their capabilities, experience, volumes and quality.
Top 10 Microwave PCB Companies
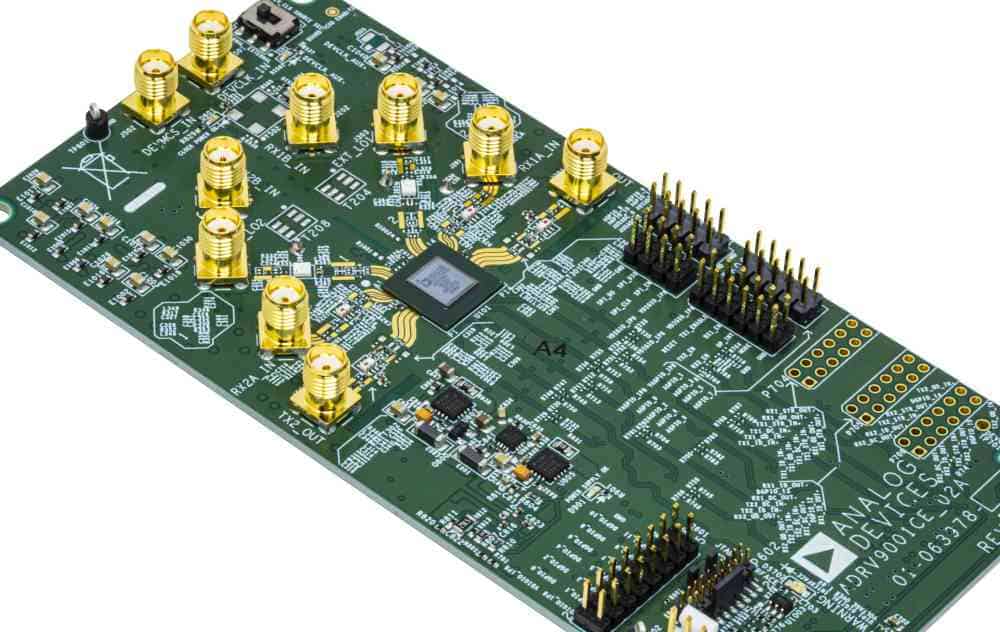
1. Rayming Technology
- Leading China-based PCB manufacturer with expertise in high frequency boards up to 65 GHz.
- Capabilities in multi-layer, HDI, RF/microwave, flex/rigid-flex PCBs.
- Serves aerospace, defense, 5G infrastructure, automotive radar, satellite communication sectors.
- Strong expertise in RF design, simulation and product testing.
- Operates advanced quick-turn fabrication lines optimized for microwave PCBs.
2. TTM Technologies
- One of the world’s largest PCB manufacturers including RF and microwave boards.
- Global footprint with factories in North America and Asia.
- Broad experience in supplying high frequency PCBs up to 77 GHz.
- Leading RF technology portfolio from single layer to complex multilayer designs.
- AS9100 and Nadcap certified microwave PCB production facilities.
3. San Francisco Circuits
- Specialist manufacturer of rigid and multilayer microwave PCBs.
- Capabilities for boards up to 70 GHz frequency, 12+ layers.
- Excellent controlled impedance, low loss, tight tolerance and signal integrity.
- Strong expertise in PTFE and hydrocarbon ceramic substrates.
- ITAR registered and ISO 9001:2015, AS9100D and Mil-PRF-31032 certified.
4. Advanced Circuits
- Leading quick-turn PCB producer also expert in high frequency boards.
- Microwave PCB manufacturing up to 50 GHz on wide variety of substrates.
- Excellent controlled impedance and low loss laminates.
- Rigid, flex, rigid-flex PCB technologies.
- ITAR and ISO 9001:2015 registered factory with stringent quality control.
5. Epec
- One of the first manufacturers of RF/microwave boards since 1968.
- PCB technologies from single layer to 20+ layer HDI microwave boards.
- In-house RF design, prototyping and quick-turn fabrication capabilities.
- Specializes in PTFE composites, hydrocarbon ceramics, quartz.
- Services defense, aerospace, semiconductor, medical and test/measurement industries.
6. Elite Electronic Technologies
- Leading provider of mission-critical and high reliability PCBs including RF/microwave.
- Rigid, rigid-flex and sequential laminations for high layer count designs.
- In-house engineering support for electrical/mechanical design.
- Capabilities for tight tolerance aerospace and military specifications.
- Able to manufacture large format (24×24 inches) PCBs.
7. Amphenol Printed Circuits
- Part of Amphenol Corporation and specializing in complex, high performance PCBs.
- High frequency boards for defense electronics, commercial microwave systems.
- Technologies for low loss laminates, tight tolerances, sequential laminations.
- On-site testing labs to validate RF/microwave performance.
- AS9100 and ISO 9001 certified factories with stringent quality control.
8. Technic Inc.
- Specialist manufacturer of mission-critical, high performance PCBs.
- Microwave boards with operating frequencies up to 50 GHz.
- Rigid, flex and rigid-flex constructions.
- ITAR registered and ISO 9001:2015 and AS9100 certifications.
- Customers in aerospace, defense, telecom infrastructure sectors.
9. Würth Elektronik
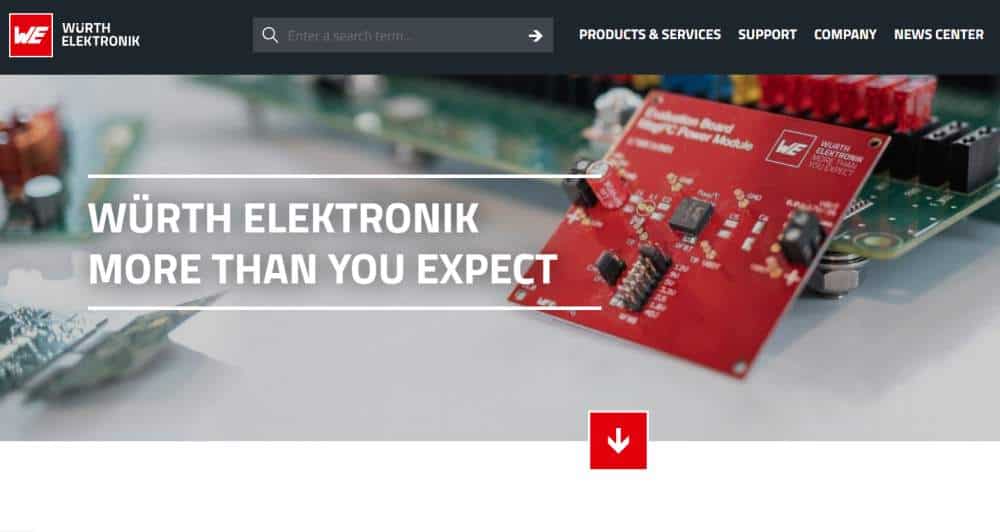
- Leading European PCB and electronic systems manufacturer.
- Producer of RF PCBs, hybrid microwave circuits, antennas.
- Offerings for telecom infrastructure, radar, traffic control, automotive markets.
- Technologies for low-loss dielectrics, controlled impedance, HDI stacking.
- IATF 16949 certification for quality production.
10. Compeq
- Major Taiwan-based PCB manufacturer with growing RF/microwave segment.
- Capabilities for high complexity boards up to 4GHz range.
- HDI build-up technologies, blind/buried vias, microvias.
- Also produces high frequency RF modules and functional components.
- Growing qualifier for 5G infrastructure related PCBs globally.
Microwave PCB Manufacturing Capabilities
Here are some of the key capabilities offered by the leading microwave PCB manufacturers:
- Multi-layer boards – Up to 20-30 layers for complex microwave circuits and antenna substrates.
- HDI technology – For high density interconnects and fine features demanded in mmWave PCBs.
- Sequential laminations – Building boards with different materials/thicknesses for optimal electrical or thermal performance.
- Low loss laminates – PTFE composites, hydrocarbons, ceramics for tight loss control.
- Controlled impedance – Tolerance as tight as ±5% for precise electrical performance.
- Signal integrity – Optimizing trace dimensions, dielectrics, ground planes to maintain signals.
- Hybrid circuits – Integrating active components, thin film elements into the PCB.
- Thermal management – Effective heat dissipation techniques for high power RF boards.
- EMI shielding – Shield cans, gaskets, absorbers to minimize interference.
- Testing – Extensive RF/microwave testing on site to validate electrical performance.
Microwave PCB Materials Used
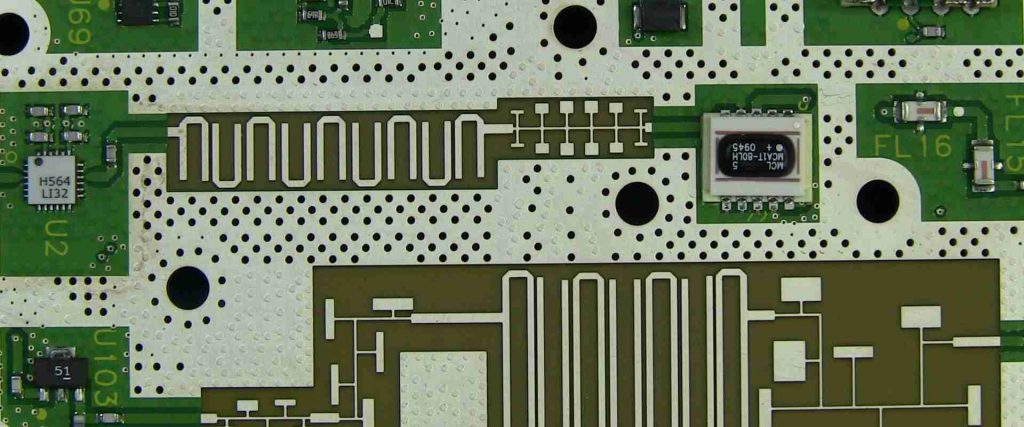
To achieve the stable dielectric properties and low loss required in high frequency PCBs, some common microwave substrate materials used are:
- PTFE Composites – Woven glass or ceramic reinforced PTFE offers excellent performance for mmWave PCBs. Examples are Rogers RO3000 and RT/Duroid 6000 series.
- Hydrocarbon Ceramics – Provides tight dielectric constant tolerance and low loss. Rogers RO4003C is a popular microwave laminate.
- Ceramic Filled PTFE – Improves high frequency performance over pure PTFE. Examples are Rogers TMM 10i and Taconic TLY.
- Quartz – Extremely low loss even at very high mmWave range. Costlier option.
- Modified epoxy resins – Provide lower cost alternative to PTFE with decent microwave performance.
Key End Applications
Some major end use segments for microwave PCBs based on their operating frequencies include:
300 MHz to 3 GHz
- WiFi equipment
- Wireless infrastructure
- Broadcast systems
- RFID, telemetry
3 GHz to 30 GHz
- Radar and satellite communications
- 5G wireless systems
- Automotive collision avoidance
- Aerospace and defense
30 GHz to 300 GHz
- Military radars and sensors
- High frequency radio astronomy
- Medical imaging
- Research lab instrumentation
So microwave boards span a wide range of wireless and high speed electronic systems in both commercial and defense applications.
Global Microwave PCB Market
- The global market for microwave PCBs was around US$ 1.3 billion in 2021.
- The RF/microwave PCB segment is forecast to grow at 4%+ CAGR over the next 5 years.
- Key growth drivers are expanding 5G and WiFi networks, satellite broadband, adoption in autonomous vehicles and increasing defense electronics spending.
- North America and Asia-Pacific are the largest regional markets currently, together accounting for over 70% of microwave PCB production.
The continued proliferation of high frequency wireless communication technologies will sustain long term momentum in the microwave PCB market.
Benefits of Partnering with Specialist Microwave PCB Manufacturers
There are several advantages of working with established PCB companies focused on high frequency boards:
- Precision manufacturing – They maintain tightly controlled processes to achieve electrical tolerances and repeatability needed for microwave circuits.
- Specialized expertise – Extensive experience in working with challenging microwave materials, constructions and testing methods.
- Quality – Stringent quality control and end-product validation required for defense, aerospace and other premium applications.
- Rapid prototyping – Quick-turn fabrication capabilities to accelerate RF product development cycles.
- One-stop-shop – End-to-end solution spanning design, fabrication, testing for simplified logistics.
- Certifications – Rigorous certifications like ISO, AS9100, or ITAR registration preferred by many top-tier microwave product companies.
- Support – Dedicated engineering teams and account management support available.
So choosing an established microwave PCB partner with proven expertise and credentials ensures access to world-class quality, capabilities and service.
Conclusion
Microwave PCB manufacturing requires close collaboration between designers and manufacturers. Companies like TTM Technologies, San Francisco Circuits and Rayming Technology offer the specialized technologies, tolerances, testing capabilities and certifications needed for defense, aerospace and other critical microwave applications. As high frequency systems continue proliferating, microwave PCBs will grow in complexity and precision. Partnering with an expert microwave PCB producer becomes essential to harness these cutting-edge technologies.
Frequently Asked Questions
What are some key specifications for evaluating microwave PCB manufacturers?
Important parameters are: frequency range, layer count capabilities, laminate materials, impedance tolerance, design analysis expertise, testing capabilities, quality certifications and ITAR/DFARS compliance.
What are the latest technologies used in advanced microwave PCBs?
Some leading-edge microwave technologies include embedded passives, additive manufacturing of conductors, laser direct structuring for fine features and 3D RF integration or packaging techniques.
What testing is required to validate microwave PCB performance?
Typical microwave PCB tests involve impedance, insertion loss, VSWR, thermal analysis, power handling, dielectric constant, moisture sensitivity level (MSL) and microsection inspection.
How are thermal issues addressed in high power microwave PCBs?
Methods like thermal vias, copper planes, embedded heat pipes, metal core boards, additional dielectric layers or strategically placed thermal pads help dissipate heat.
What design principles help improve microwave PCB performance?
Careful stackup planning, adequate shielding, impedance matching, minimizing stubs/discontinuities, ground plane discipline and simulated results validation are key microwave PCB design practices.
Top 10 Microwave PCB Raw Materials In The world
While designing PCB components at higher frequencies, a conductivity constant (DK), overindulgence feature, thermal expansion coefficient (CTE), dielectric constants, and current conductivity are key characteristics that define laminate circuit performance for microwave/RF printed circuit boards.
Polytetrafluoroethylene (PTFE) is the most recognizable different frequencies material for workers of PCB covers. It has good dielectric characteristics for radio waves and is a fabricated thermoplastic fluoropolymer. Here is a short overview of the key material suppliers with whom we have the expertise; all the material is handled inversely, and it is important to know how the components will react to all processes precisely.
Many factories have a considerable stock of all HF laminates since they have manufactured PCBs using those factual for the past many years. The RF antenna, the Wi-Fi, the IP backbone, optical switches, diplexers/multiplexors, signal processing, and many others are among these PCB applications.
It is vital to have substantial expertise in the production of PCBs from these items and also to invest in equipment for the correct processing of these microwave PCBs. PCBs created from these items are crucial.
Manufacturing and CAM experience are crucial to guarantee that your PCB is constructed to endure since various materials have extremely varied scaling factors, as well as the reality, is that they are all variable. Without an appropriate enrollment, coating deposit shirt, and additional aspects utilizing the right equipment such as X-ray, it would be impossible for manufacturers to get the yield that provides the consumer trust.
1. Materials from Rogers:
As being the oldest world’s major public corporations, Rogers offers a wealth of inventive and collaborative approaches for problem-solving with consumers. Rogers, in 1949 created the first material for RT/duroid® in electronic appliances, and now RT/duroid® is the market leader in great-speed microwave PCB enterprises in the High-Frequency PTFE family. “Helping our world, protecting and connecting our planet” is the slogan of the Rogers Organization. The team combines a complete range of solutions from any PCB manufacturer using sophisticated Rogers’s products with the application experience, worldwide resources, and engineering and design capabilities of Epic.
Most laminates of PTFE PCB require specific materials and systems in order to produce the best accuracy of PCBs together with substantial capability in the material stuff, as many substances differ during PCB handling. Teflon is the most famous brand name for PTFE-based formulations.
It is utilized in modern non-stick pans so that it might be hard to deal with this material if you don’t have the right knowledge.
2. Panasonic MEGTRON 6
Panasonic MEGTRON 6 is a sophisticated laminate circuit board technology for induction motors such as grid equipment, data centers, IC testing systems, and high-frequency measurement equipment. MEGTRON 6 is well recognized for its low dielectric dissipation and dielectrically factors, low transmission loss, and strong thermal expansion.
3. High-performance material from Isola:
Isola has been a pioneer in the development and manufacture of copper laminate solutions for the production of innovative multi-faceted circuit boards (PCBs) since 1912. When choosing basic materials, they have an optimum combination between price and efficiency. Microwave and millimeter-wave designers must take into consideration key criteria in their choice of increased RF or microwave laminate involving dialectical thickness, dielectric constant factor and dissipation factor, and high quantity tolerance. Microwave
High-frequency circuits need exceedingly accurate steady dielectric, layer thickness, and dielectric thickness management. The following table includes some of the common prevalent laminates of Isola.
4. Higher Dk Materials:
When searching for PCB materials for LNAs and PA, circuit materials with greater Dk values may be used for a certain impedance and frequency range to miniaturize the circuit dimensions when they are physically critical.
Circuit wavelength is dependent on frequency and material, and PCB substances with higher values of Dk lead to the operation of routing algorithms at lower frequencies at a given frequency.
The use of higher-Dk circuit materials may result in smaller PCBs for a range of wavelength-dependent circuit devices, such as antennas and filters. Conventional PCB materials are usually within Dk ranges 2 to 6 for microwave applications, such that “high-Dk” board materials are commonly regarded to be Dk 6 or above.
5. Arlon Electronic Microwave PCB Materials:
Arlon Electronic Resources specialized in the acrylate resin technique, which included polyimide, extraordinary-TG, and low-cost thermoset laminate structures, and Arlon was recently acquired by Rogers Corporation. These resin alternatives are designed on a range of substrates like fabric crystal and non- plaited aramid, which are utilized for high-speed, reliable microwave PCB trails. Applications that are highly exposed to high heat such as aeroplane instruments, down-holes, and RF antennas are often ideal choices for Arlon supplies.
6. PA Materials:
The RF/microwave PA circuit materials have a slightly distinct set of important criteria since they handle much greater power values than LNAs.
Tight Dk and susceptibility control are, as with circuit elements for LNAs, significant factors for materials evaluated for PA circuits. Due to the additional heat created by these kinds of amplifiers, thermal conductivity is a little more significant for PA designs. In reality, the essential PCB material properties for PA are thermally connected, including heat capacity, TCDk, and thermal expansion coefficient (CTE).
7. Taconic Microwave Materials:
Since 1961, Taconic has become a global superpower in PTFE products. They provide a variety of best applications today with PTFE and silicone-covered materials, tapes, and panels. CTE PTFE laminates with a thermally stable, the main focus for Taconic equipment used in RF/microwave PCB manufacture are low DK. Many Taconic devices have been engineered to provide world-class loss-insertion capabilities with an ultra-low fiberglass percentage and uniform refractive index across the cover.
The homogenous ceramic dispersion during the enclose produces extraordinarily low thermal expansion X or Y constants. For each use, Taconic provides materials and a shortlist of its offers.
8. Metal Material for Microwave PCB:
Copper, aluminum, iron, etc. conventional materials are still employed in PCBs. These materials enable the use of such Surface Mount Technology (SMT) for perceptions associated. Mechanical durability is also provided. The lifetime of the metal base PCBs is therefore much longer.
The various materials for the development and installation of PCBs all offer a range of advantages and drawbacks. The material is selected considering the application, the necessary outcome, environmental considerations, and any other restrictions faced by the PCB. You should choose the material of the PCB according to the expected results.
9. FR-4 Material:
This is the material most often used in PCBs. It is a laminate epoxy strengthened in the glass. The epoxy is mostly flammable and waterproof. It provides significant weight strength. This material has a very high tensile strength.
10. PTFE (Teflon) for Microwave PCB:
PTFE is a kind of polymeric substance that provides no resistance and is thus employed in high-speed applications with a high frequency. PTFE is very flexible, which makes it important in tight tolerant applications. It is also highly lightweight and may be utilized in numerous sectors. It is also flame-resistant, has a high physical prowess, offers stability to the temperature, and is diverse in use.